Last Sunday was a day that I had been looking forward to for a long time. I first discovered the “Zentralwerkstatt” – the central maintenance depot – in Frankfurt some years ago by chance.
I was curious as to where the lines went past the end of the last U-Bahn station, as they followed the road and suddenly disappeared behind a set of iron gates. Google Maps provided the answer – behind those gates lies the depot where the trams and the U-Bahn trains go in Frankfurt when they need servicing or repairing. There is even a 800m long running track to test them on.
So when I read about an open day I grabbed the chance to visit the site and take a look around.
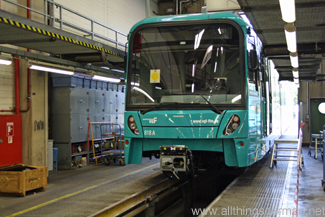
The end of the U5-50 train over a maintenance pit
On what was one of the hottest days of the summer so far, the grounds had been turned into a mixture of trains and their components to see and a childrens’ playground with refreshments.
We started by taking a look around the workshop, where one of the new 50m flexible (U5-50) trains was stationed. It was the first time that I had been able to walk the entire length of one, as I had not actually been on one in normal service.
The next train was set to allow people into the driver’s cab, and although it was not going to be going anywhere, some of the functions like the horn and the indicators were working, much to the delight of many teenagers.
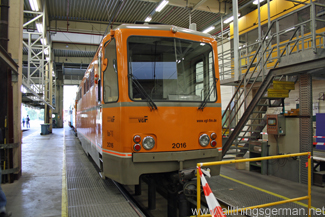
Permanent Way unit 2016
It was particularly interesting to be able to see some of the permanent way vehicles, especially driving unit 2016 which has a connection to Oberursel. It is was built on tram bogies with batteries taken from the 2020 locomotive which is currently stabled in the Bommersheim depot.
One of the other trains in the shed was driven out by one of the VGF drivers for a very special reason. Each hour 15 people were being picked to actually drive the train on the test circuit. To take part you needed to answer four questions, with different questions being posed for children and adults. The childrens’ questions were so easy, that my daughter answered them without any problem. The adults’ questions were certainly more difficult and required you to know quite about about train company.
As it turned out, in the first draw of the day my daughter’s name came out of the box first! (Or as she would point out, her entry was the first one out with all the correct answers on it). And so it was, that we made our way to the waiting U-Bahn unit (type U5 made by Bombardier) to climb up into the cab. Once she had got the hang of the dead man’s handle we set off around the test track until we came to the junction with the incoming service line. At this point we walked down the length of the train to the cab at the other end and she took the train back to where we had started from. The was surely the highlight of her weekend!
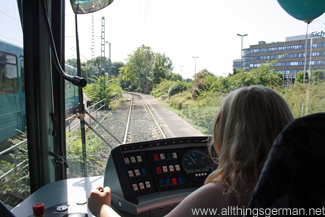
Driving a train around the test track
We made it back to the entrance to the shed in time to see a demonstration by the Frankfurt fire brigade of how they lift a derailed tram back onto the tracks. This is done with special hydraulic equipment that is carried by a dual-wheeled vehicle. One set of wheels has normal tyres on it, the other has flanges to allow it to run on the railway lines. Of course, in order to demonstration how to lift the tram onto the tracks, they had to lift it out of them first. Amazingly, once the hydraulic lift is under the front of the train, it can just be swung back and forth. As easy as this may sound, it took a lot of precision work on behalf of the fire brigade to get the train that far. And before they even started they secured the rear of the train to make sure that it didn’t just roll backwards off the lifting gear.
As interesting as this was to watch, with so many children present it would have been nice if someone could have given a commentary on what was actually happening.
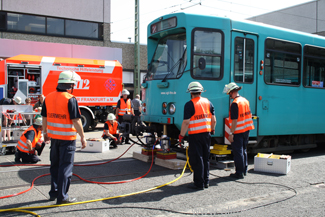
The fire brigade de-rail and then re-rail a tram.
However lack of information is one thing that certainly cannot be said about the guided tour of the workshop which lasted just over an hour.
One of the VGF employees took us through each part of the building explaining both the different types of trains being serviced or repaired as well as which work was carried out in which areas. Together this gave some idea of the process that a train goes through when it is at the workshop.
We started the tour outside of the “entrance” – four tracks where the trains enter from the service line and first go through a series of checks. They leave via the same tracks later after quality control checks have taken place.
From here they are transferred using a moving platform (“Schiebebühne”) – like the bridge of a turntable, but rather than turning it goes back and forth with the exits lined up instead of in a circle.
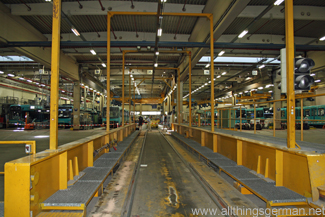
The Schiebebühne
These exits led to specialised areas for paint spraying, washing, lifting the carriages off their bogies, or just simply stripping the units down for their 8 year inspection, during which almost every part of the train is removed and either checked, replaced or upgraded. For example, the “U4” type of trains are currently being upgraded so that their livery matches that of the “U5” (eg. the yellow strips on the doors) and having security cameras inside the carriages added. All of which is time consuming work: an 8 year service takes 140 days to complete. Just spraying paint on a 25m long train takes 4 days!
Particular attention was given to the areas where new sets of wheels and bogies were stored with an interesting statistic. The wheels have 60mm of metal on them that gets worn down over time. How long this takes obviously depends on the route that the train is used on, but the average is between 7 and 8 millimeters per month. So allowing for a safety margin that means that each carriage needs its wheels changed twice a year!
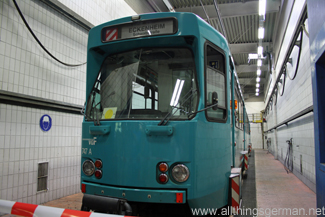
The tram wash
And it is not just the regular servicing that goes on in the workshop, damaged trains that have been in accidents get repaired there as well. The number of accidents per year on the network in Frankfurt was given as between 360 and 400, although this includes everything from a scratch in the paintwork to a complete write-off. Anything that cannot be done in one of the depots gets taken to the central workshop.
Having seen all of the areas with rails, the tour finished inside a room full of tools where the spare parts are made. Amazingly 95% of the spare parts required to repair or upgrade the trains are made on-site, meaning that not only do the technicians not having to wait long times for suppliers to deliver, but that the quality can be tightly controlled as well.
We learnt a lot on that tour, which will probably only serve to increase my fascination with the U-Bahn line in Oberursel. But for my daughter the best part of all was probably sitting in the cab and actually driving one of the very trains that she normally only gets to ride in.
We would like to express our thanks to the VGF for allowing us to publish the photos of their workshop and the open day on this website.
Speak Your Mind